A digital control amplifier from a C-130 Hercules was recently sent to a repair depot to replace damaged handles. These handles allow the amplifier to be locked into its proper place on the aircraft. Without properly operating clamping handles, the apparatus was not mission ready. Without an operational backup, the Hercules would be categorized Aircraft on Ground (AOG). (See Broken Handle in Figure 1)
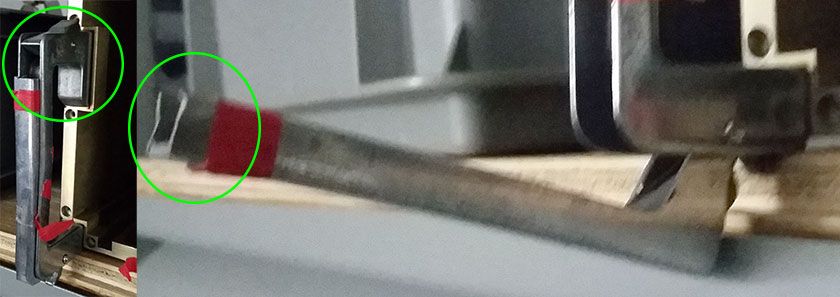
Broken Handle – Figure 1
As a purchaser or buyer in the aerospace community, you may be tasked with identifying a qualified repair facility that could correct the damaged part. The handle repair not only needs to meet the exact specifications for fit, form or function, but also requires a competitive price and a quick turnaround to return the component back to service.
You need to feel confident that a supplier or repair depot of the handle can meet or exceed the standards and specifications necessary. The original cast aluminum handle is no longer produced, but the repairing company can mill an exact replica in aluminum. How do you know that the new part will operate properly within the same tolerances as the original?
With the globalization of your supply chains being affected by their own regional and national requirements, it becomes more complicated for you to ensure the final product your supplier delivers to you meets requirements. The repairing agency will need to provide you objective evidence that all engineering design and specification requirements are understood, accounted for, verified, and documented. The initial runs of the manufactured handles should be evaluated to assure that it conforms to the specified standards, procedures and contract requirements.
To achieve this goal, the tool you require from the repairing agency is a document called a First Article Inspection Report (FAIR). The FAIR consists of measuring the properties and geometry of an initial sample item against given specifications. In this example, without an existing supplier still manufacturing the handle, the repair depot reverse engineered a properly functioning handle based on the requirements and specifications of a properly operating handle. (See Repaired Handle in Figure 2)
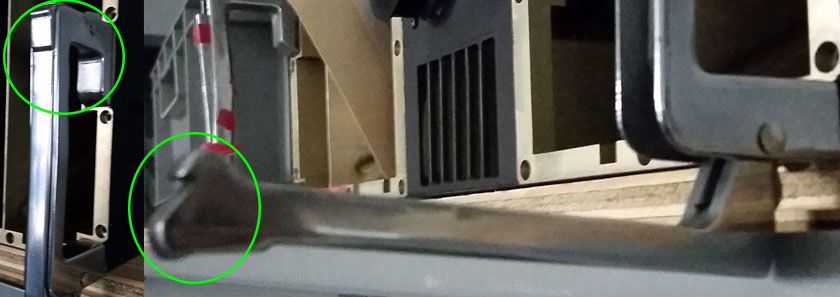
Repaired Handle – Figure 2
The FAIR provided to the buyer should be based on an item in the first production lot. Despite its name, the item inspected for the FAIR does not need to be the very first one produced. A FAIR is typically required on all aerospace and engineering contracts between a buyer and a producer of a manufactured product to ensure the reliability of the production process.
When a First Article Inspection is Required
- New parts/products released to production.
- A change in the design that affects fit, form or function of the product.
- A change of the manufacturing source or process. Also, if the inspection method, location of manufacture, tooling or materials, that will affect fit, form or function.
- A change in a computer generated program that affects fit, form or function.
- A natural or manmade event that affects the manufacturing process
- A lapse in production for a period of 2 years, or as specified by the customer
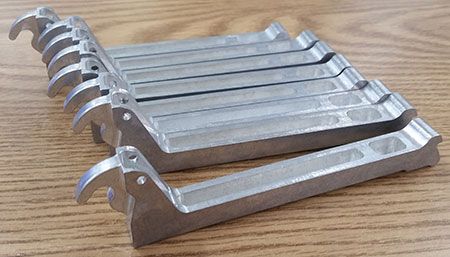
Fabricated Handles -Figure 3
In this instance, Duotech produced this handle for the repair that is the subject of this article. A previous First Article Inspection was successfully conducted on a similar system, and the new handle manufactured and repair of the digital amplifier was completed. Three years later, a different digital amplifier was in need of the same repair. Since the last item was produced over two years ago and the manufactured source would change from a mill to a gantry, a new FAI was required. DSI successfully completed a new FAI and the repair was approved by the customer. (See Fabricated Handles in Figure 3) The digital amplifier was then repaired and returned to the customer.
Other Examples
New Product from an Existing Product – In a recent repair, Duotech needed a spring to correct a broken clamp that held a circuit board in its proper place. A Commercial Off-The-Shelf (COTS) product meeting the exact length specification did not exist. Duotech had several springs in stock that were longer than was required. DSI Technicians shortened the existing spring to fit under the clamp for the circuit board. Since an existing product (long spring) was shortened, it became a new product with a new part number and required a FAIR, which was provided to the customer. Once approved, the new spring was put in place, the board repaired and returned to the customer.
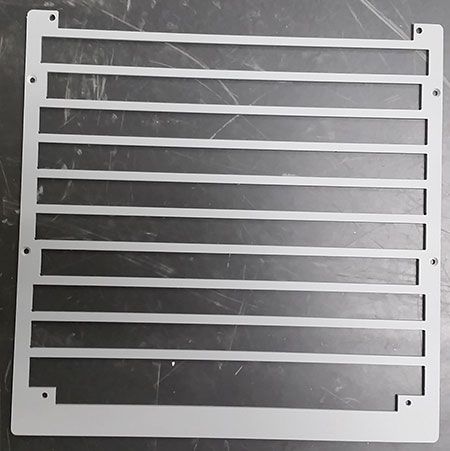
Heat Spreader – Figure 4
New product for Delta Radar Upgrades – In order to transfer heat from a circuit board in Duotech’s new radar upgrade capability, DSI manufactured a new product called a heat spreader (See Heat Spreader in Figure 4). This new item, like others engineered and released for production to upgrade radar system like the APG-66, APG-68 and the APQ-159, required a First Article Inspection to ensure Duotech can repeatably produce a product that conform to fit, form, and function requirements within radar system LRUs requiring upgrade.
Monitor Suppliers Using First Article Inspections
As a buyer, it’s important for you to maintain a strong supply chain. You need confidence that your suppliers correctly understand all the requirements and are producing quality products that meet specifications necessary for you to maintain your mission. Requiring First Article Inspections on all new products, and following-up on reviews, ensures that suppliers meet specifications for fit, form or function.
Put Duotech Into Your Supply Line
As part of our quality management system (QMS), Duotech is AS9100 and ISO 9001 certified. Duotech produces numerous items as stand alone products, like our Digital G-meter and subassemblies of larger assemblies like the Delta Radar Upgrades.
At Duotech, reverse engineering and fabricating one-of-a-kind machined parts from aircraft grade 6061 or 7075 aluminum alloy is a daily requirement. In order to meet the requirements of AS9100, meticulous attention to accuracy and precision is required.
From concept to implementation, Duotech’s capabilities encompass your entire project. On-site machining and fabrication shortens design cycles. Our staff puts time on your side. Whether J.I.T. or build-to-print, send us your requirements for aerospace quality work.