Terms and Conditions for Suppliers of DSL
- Where required on Duotech Services, LLC.’s (DSL) Purchase Order (PO), suppliers must use DSL’s customer-approved special process sources.
- Suppliers must contact DSL in the event of the discovery of nonconforming product/material. Arrangements for the approval of supplier nonconforming product/material must be as directed by a DSL authorized representative.
- Suppliers are required to notify DSL of any changes to a product and/or process and to obtain approval from an authorized representative prior to implementation (if applicable).
- DSL, its customers, and regulatory authorities retain the right of access to all supplier facilities involved in this order and to all records related to this transaction within eight (8) years after final payment.
- DSL requires that its suppliers flow down all applicable AS9100/customer/regulatory requirements to any sub-suppliers (including requirements in the Purchasing documents and key characteristics where required).
- DSL performs inspection activities at our facility to ensure that purchased product meets all applicable purchasing requirements.
- When DSL or its customer intends to perform verification at the supplier’s premises, DSL will first state the intended verification arrangements and the method of product release. This information will be communicated on the DSL PO.
- Where specified in the contract, DSL’s customer or customer’s representative will be afforded the right to verify at the supplier’s premises and DSL’s premises that subcontracted product conforms to specified requirements. Verification by the customer is not used by DSL as evidence of effective control of quality by the supplier and shall not absolve DSL or its supplier of the responsibility to provide acceptable product, nor shall it preclude subsequent rejection by the customer.
- To prevent the purchase of counterfeit or suspect/unapproved products and to ensure product identification and traceability, DSL requires supporting documentation from its suppliers:
- Supplier shall establish and maintain a Counterfeit Parts/Material Control Plan using AS6174 std and/or AS5553 std.
- Unless otherwise specified on the purchase order, all suppliers shall provide a Certificate of Conformance for each product purchased by DSL. All metal raw materials supplied to DSL must be accompanied by Material Certificates.
- Suppliers must warrant that only new and authentic materials are used and supplied to DSL at all times. Any counterfeit parts detected shall be reported to GIDEP and DSL.
- In order to mitigate the risk of unintentional use of counterfeit parts, the supplier shall obtain parts only from Original Manufacturer, authorized aftermarket manufacturer, or authorized distribution chain unless otherwise approved in writing by DSL.
- DSL will not accept parts or materials procured from any of the following companies:
- HONG DARK ELECTRONIC TRADE COMPANY
- HONG DARK ELECTRONIC CO., LTD
- HONG DARK ELECTRONICS CO., LTD
- HONGDARK ELECTRONIC CO., LTD
- HONGDARK ELECTRONICS CO., LTD
- SHENZHEN HONGDARK ELECTRONICS CO., LTD
- HONGDARK ELECTRONIC
- HONGDARK TECHNOLOGY CO., LIMITED
- HONGDARK
- HONG XING DA TECHNOLOGY CO., LTD
- VISIONTECH COMPONENTS
- VISION TECH
- WESTERN TITANIUM INC
- CAL TEX
- BASIC RUBBER.
- Records are available for review by customers and regulatory authorities in accordance with contract or regulatory requirements.
- DSL may also require specific actions where timely and/or effective corrective actions to a supplier issue(s) are not achieved. These actions may include, but are not limited to, any or all of the following: withholding payment until the issue is resolved, removal of the supplier from DSL’s Approved Supplier List, and other legal actions.
- All limited-life items must have a minimum of 75% life remaining upon receipt at DSL, per limits established by the Aerospace Standard for age control (shelf-life), SAE AS 1933 and SAI ARP 5316, or the manufacturer or MIL-HDBK-695. For limited-life items one of the following is required:
- Cure date
- Date of Manufacture and Shelf Life
- Expiration Date
- If applicable, the manufacturer’s name and batch/lot number are required.
- Suppliers must provide current MSDS (Material Safety Data Sheet) for every hazardous material or chemical supplied to DSL.
- Suppliers of electronic components or other Electrostatic Discharge (ESD) sensitive materials shall use an ESD awareness program based on ANSI/ESD S20.20 or better.
- Any type of fraud and falsification activities will be subject to applicable Federal penalties.
- Suppliers and any sub-contractors shall ensure that persons are aware of their contribution to product or service conformity, their contributions to product safety, and the importance of ethical behavior. DSL requires that supplier personnel be adequately trained and/or qualified to perform the work required under DSL POs. When required by our customer, DSL may specifically designate the requirements for training and/or qualification on the PO.
- If, at any time, the supplier is unable to adhere to the requirements specified on this page it is mandatory to notify DSL’s cognizant representative. Unless otherwise stated on the DSL PO, the supplier shall communicate directly with the DSL point of contact designated on the PO. Acceptable forms of communication are via phone, fax, and email with the designated DSL point of contact.
- Unless expressly accepted in writing by DSL, additional or differing terms or conditions proposed by the customer or included in the customer’s acknowledgment are objected to by DSL and have no effect.
- DSL Quality Department actively monitors, reviews, and rates supplier performance on an ongoing basis. Ratings are based on delivery, pricing, and product/service quality conformance, in addition to supplier quality certifications. The supplier’s current ratings appear on the POs. The rating system is from 1 – 10 with 10 being the best possible rating. Ratings of 3 or lower require specific DSL management approval.
- Suppliers are expected to control and monitor their suppliers’ performance and use customer designated/approved suppliers, including process sources when specified in the contract.
- Suppliers are to implement a Quality Management System to provide for continual improvement of their processes, products, and services.
- DSL is committed to maintaining the highest level of service, safety, and ethical standards. Our suppliers are essential to delivering the critical parts and services that DSL provides to our customers. They are critical to our shared success. We are committed to developing and maintaining partnerships with suppliers who are also committed to this goal. As such, we also expect our suppliers to understand their role as team members and to maintain the same standards we apply to ourselves. This includes a responsibility and commitment to ensuring product safety throughout the product realization process, including the safety of supplier personnel and the product itself.
Above all, it is essential that our suppliers maintain the highest standards of ethical behavior in support of our needs. DSL shall not accept any unethical behavior on the part of our suppliers. This includes falsification of any information, harassment, kickbacks, workplace violence, money laundering, or any other behavior forbidden by statutory law in the United States. Failure to comply with these standards may result in decreased supplier ratings or permanent debarment as a DSL supplier. - When required by our customer and DSL Purchase Order, DSL, and our suppliers shall use statistical techniques for product acceptance along with instructions on the performance of such practices.
- DSL shall provide specific design and development requirements, critical items, or key characteristics as needed along with the PO, when required.
- Suppliers may be required to provide test specimens for design approval, inspection & verification, investigation, or auditing. Such requirements shall be included in the PO.
- FOD prevention Program requires a QAP per NAS412.
- Not withstanding any prior executed agreement, DSL shall have the right to terminate any Purchase Order, in whole or in part, at any time without cause, regardless of dollar value, by providing written notice to the Seller. Upon receiving notice of such termination, Seller shall:
- Stop all work under this Purchase Order on the date and to the extent specified;
- Place no further contracts hereunder except as may be necessary for completing such portions of the Purchase Order as have not been terminated;
- Terminate all contracts to the extent that they may relate to portions of the Purchase Order that have been terminated; and
- Protect all property in which DSL has or may acquire an interest and deliver such property to DSL.
- DSL’s sole obligation to Seller in the event of a termination for convenience shall be to pay Seller a percentage of the Purchase Order price corresponding with the percentage of the terminated work actually performed prior to the notice of termination, plus Seller’s reasonable expenses incurred as a direct result of the termination. Under no circumstances shall Seller be entitled to anticipatory or lost profits. Within twenty (20) days from such termination, Seller may submit to DSL its written claim for termination charges in the form prescribed by DSL. Failure to submit such claim within such time shall constitute a waiver of all claims and a release of DSL’s liability arising out of such termination.
DSL reserves the right to verify claims hereunder and Seller shall make available to DSL, upon its request, all relevant books and records for inspection and audit (e.g., timecards and receipts). If Seller fails to afford DSL its rights hereunder, Seller shall be deemed to have relinquished its claim.
Effective Date: October 1, 2024
Our Certifications
Duotech maintains an AS9100D + ISO 9001:2015 registration with the scope of repair, design, production (including CNC machining and laser cutting), testing, and overhaul Services for electronic and electromechanical equipment for military and commercial applications.
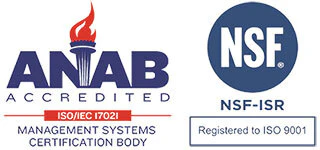