Close to the end of a day, a shipping manager at an aerospace and defense company sits at his desk entering customer asset data into an internal data management system. He hears a horn blow and looks up to a monitor above him to see a shipping truck backing up to the rear dock outside. The truck is late and the manager is less than enthused. He angrily drags a pallet jack behind him and heads to the shipping door – he expects this shipment to include a heavy APG-66 radar system in a big bulky crate.
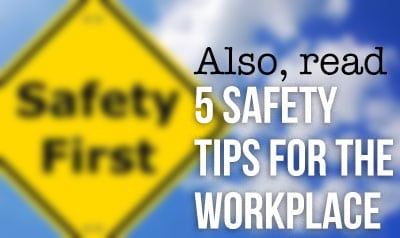
Also, read “5 Safety Tips for the Workplace“
The manager’s temper is short because the driver is unapologetic. He hurries to get the crate off the truck. He has difficulty maneuvering the pallet jack into place quickly, and, lacking patience, reaches down to grab the edge of the pallet to jerk it into position.
As he pulls the wooden pallet he feels a quick, sharp pain in his lower back and also runs a big splinter into his index finger.
Now he is mad, injured, and can’t stand up straight.
As the large component moves from the truck, through shipping, to the repair technician’s station, its journey through the maintenance, repair, and overhaul process is completely documented. With procedures in place for the accountability, handling, and technical requirements of the repair of electronic and electro-mechanical equipment, the company ensures compliance to maintain their AS9100D certification.
Safety First
When it comes to employee safety, what about the proper handling of the large wooden crate that houses the antenna? What safety precautions should the shipping manager and other employees apply to avoid scrapes and cuts, crushed toes, or back injuries, as well as moving the crate in a manner that protects the customer asset?
Below we share safety tips when handling materials. Safe lifting and handling of big, bulky boxes and crates must be done in compliance with the Occupational Safety and Health Administration (OSHA) guidelines. For a more in-depth understanding of your company’s policies for customer asset and hazardous material handling, you should refer to your company’s Quality Assurance Manual.
6 safety precautions when moving heavy materials manually
- Safety Equipment – Workers should always wear appropriate personal protective equipment. Wear gloves and long sleeve shirts for forearm protection when lifting items that have sharp or rough edges. Protect your vision with safety goggles. When lifting items that are very heavy, you should wear steel-toed safety shoes or boots to protect your feet and toes.
- Lift Properly – Use proper lifting techniques: bend at your hips and knees to squat down to your load, keep it close to your body, and straighten your legs to lift. Consider wearing a lumbar support belt for spine support and encourage leg lifting.
- Add Handles – When moving materials manually, workers should attach handles or holders to loads.
- Get Help – When an oversized load is too bulky to properly grasp or lift, get a co-worker to assist you to reduce risk to yourself and avoid damaging the material. If you cannot see around or over the load, seek help from another employee to help you move the material safely.
- Blocking Materials – Use blocking materials that are large and strong enough to support the load safely. Blocking material should be in good condition, and not have cracks, be splintered, or dry rotted. When placing blocking material under a load, be cautious that load is not released before removing hands from under the load.
- See OSHA’s Booklet – For more details about Materials Handling and Storage visit OSHA’s website.
Workplace safety is important in all industries. In the aerospace industry, a shipping department will encounter many hazardous materials, be responsible for expensive equipment that is often obsolete and hard to replace, and move containers that can be very large and heavy. Protecting yourself, your employees, and your customer assets is very important to accomplishing your mission, and your customer’s.
Read also 5 Safety Tips for The Workplace
Establish Procedures
If your company does not have a quality manual in place, or material handling procedures that all employees should observe, establishing one should become a priority. Once complete, schedule training sessions to ensure all employees know what is expected when handling materials safely and how to perform them properly.
Attention To Detail Provides Quality and Safety to Our Customers
Duotech is a qualified FAA Repair Station and maintains AS9100C and ISO 9001 certifications with the scope of repair, design, production (including CNC machining and laser cutting), testing an overhaul services for electronic and electro-mechanical equipment for military and commercial applications. If you need an item repaired search our extensive support capabilities database. If you need to request a repair quote, we make it easy.