Supporting the Past. Engineering the Future. Repair. Reverse Engineer. Renew.
Duotech is a trusted, requirements-driven company structured to solve the modernization, engineering, reverse engineering, repair, sustainment, and re-manufacturing problems of military and civilian agencies, as well as aerospace and commercial users of electronic and electromechanical equipment.
We save our clients millions of dollars annually by providing expert aftermarket services for their legacy electronics systems, increasing defense platform operational availability, and helping clients free up time, money, and resources to apply to other initiatives. Whether it is repair of embedded electronics, designing and building market-leading automated test equipment (ATE) solutions to resurrect and optimize a test bed, or building advanced RADAR and electronic warfare (EW) products, we are typically faster and more cost-effective than what many clients could achieve using their own organic resources.
The Duotech Advantage
Cost effective
Agile with rapid execution capabilities
40 years of industry experience
12,000 unique NSN repairs completed
40 U.S. allies supported worldwide
Horizontal integration across service segments
Vertical integration from circuitry design to line replaceable unit (LRU)-level platform integration
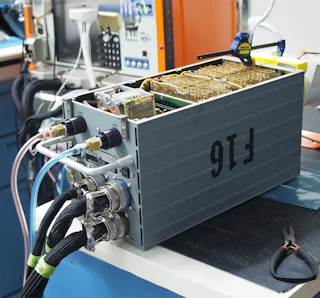
Duotech specializes in repairing and modernizing legacy equipment critical to the operation and success of military and civilian systems. Decades of industry expertise and knowledge of current trends, combined with advanced technology and best-value products has positioned Duotech as a premier partner to strengthen and enhance end-user operational capability.
SERVICES